Barriers to Fast-Charging Lithium Batteries
Thought Leadership
Fast charging is critical for global electrification
The rise of electric vehicles (EVs) is undeniable. But one major sticking point remains: charging times. Add to that the lack of available EV charging locations and short range associated with many electric vehicles, it’s no wonder that electric vehicle adoption is happening slower than hoped.
Frustration with slow charging doesn’t only apply to EVs. Speed in charging cells is a necessity for devices that cross multiple industries, such as commercial energy storage systems, power tools, mobile phones, and even earbuds.
With all the recent advancements in battery cell chemistries and designs, why is truly faster charging still not widely available? Where is the charging solution that enables faster charging in multiples, not percentages, that can work for every battery and application – and what is standing in the way?
Lithium battery tear-down conducted in Iontra labs
Li-ion battery basics
The majority of today’s products primarily rely on lithium-ion (Li-ion) batteries. As scientists and researchers began to study this new element, its light weight relative to other elements, coupled with it’s electrochemical potential made pointed to compatibility for applications in energy storage. Though initial experiments using lithium for batteries posed multiple hurdles, this changed in 1980, with the discovery of lithium cobalt oxide was used as a cathode material
This new cathode allowed lithium ions to be reversibly intercalated. This game-changing development served as the catalyst for the creation of the first lithium ion cells. Sony recognized the potential of this technology, and after investing in it’s development, released the first commercialized lithium-ion batteries in the early 1990s.
The charging challenge: disadvantages of faster charging speeds
When exposed to high charge currents, Li-ion batteries, in particular its anodes, begin to experience increased rates of damage through:
Loss of capacity: Due to temperatures within the cell, environmental factors, and use over times, the cell’s capacity will drop, decreasing functionality.
Plating: Lithium ions begin to deposit on the surface of the battery anode (negative electrode) unevenly, forming stalagmite-like structures. Once these protrusions grow to a certain size, they can puncture the separator, leading to internal shorts and subsequently, safety hazards.
Heat: Higher charging rates produce additional heat, which can speed up degradation within the battery and shorten its overall cycle life.
New cell chemistries to overcome the charging challenges
The key to faster charging lies in the battery’s technology. However, this poses some significant hurdles to overcome. Until recently, the broader scientific community thought that the only way we could extract greater performance output from batteries was through changing the structure, design, and chemistry of the batteries. Scientists are tackling these challenges on multiple fronts:
Electrode Materials: New battery anode and cathode materials capable of delivering faster charge rates are constantly being vetted. However, for any promising material that demonstrates a propensity for faster charging, the researchers must still consider and balance the effects on safety, cycle life, and energy density.
Electrolytes: The electrolyte solution that carries ions between electrodes is crucial. New formulations with higher ionic conductivity could improve charging rates while maintaining safety.
Solid-State Batteries: Solid-state batteries use a solid electrolyte instead of a liquid one. This could enable faster charging and improved safety due to reduced flammability.
Many of these new cells are still in the research phase of development, and will not be generally available for years to come.
The cost of battery innovation
From what we’ve covered so far, many of the world’s largest cell OEMs and most renowned battery research labs are searching for solutions to charge quickly and maintain stable performance by creating new fast charging batteries. However, new cell chemistry development can take decades, and have an exceedingly high cost of development, occurring at every stage.
The cost of developing new fast charging batteries
Research and Discovery: When exploring new materials, understanding their behaviors, and testing their potential, there is a need for specialized equipment, personnel, and computational modeling. Teams must also cover the cost of purchasing the materials, which depending on their rareness, can be expensive.
Initial Prototyping: This stage involves building specialized cells and testing them to assess various metrics such as charge speed, cycle life, and safety. This requires charging and discharging the cell over and over again until substantial data is returned, requiring specialized equipment, environments, and consistent access to power.
Manufacturing: If the cell passes these first two stages, the next hurdle is devising a commercialization plan to make these cells available at the needed scale. This requires the development of manufacturing infrastructure, processes, facilities for fabrication, and specialized teams.
Certifications and Approvals: Before a cell is approved for commercial distribution, they must pass multiple safety assessments and regulatory standards, which is a long and costly endeavor.
The overall cost and time commitment of developing new fast charging batteries serves as a huge barrier to research and development. Initial investments can start in the millions, and even reaching the level of billions, just for individual cell production. When a company or lab is looking to create a battery pack using these cells, the testing and validation requirements only grow.
But the burden is not only on the new cell’s creator, additional costs also fall to the companies looking to implement them.
OEM costs for implementing new cell chemistries
Procurement Costs: Depending on the rarity or novelty of the battery materials used, the cost per cell may be more expensive than the cells the OEM is currently using.
Product Integration: If an OEM decides to use a new cell with a different size, shape, or desired characteristics, the product itself may require redesign. This means that the OEM will have to modify the product’s internal components, and in extreme cases, it’s functionality, which incurs engineering costs.
Manufacturing: Once the product modification is complete, changes may need to be made to the OEM’s assembly lines, which can require new or additional equipment and personnel training. This transitionary period can also result in downtime, which is costly.
Managing inventory: OEMs will need to separate their inventory of old and new product models, and maintain these holding spaces during the transition period, which puts a burden on logistical processes.
Supplier Relationships: If a new cell is being used, this requires establishing a new supplier relationship, which can incur additional expenses for qualifying the supplier’s offering.
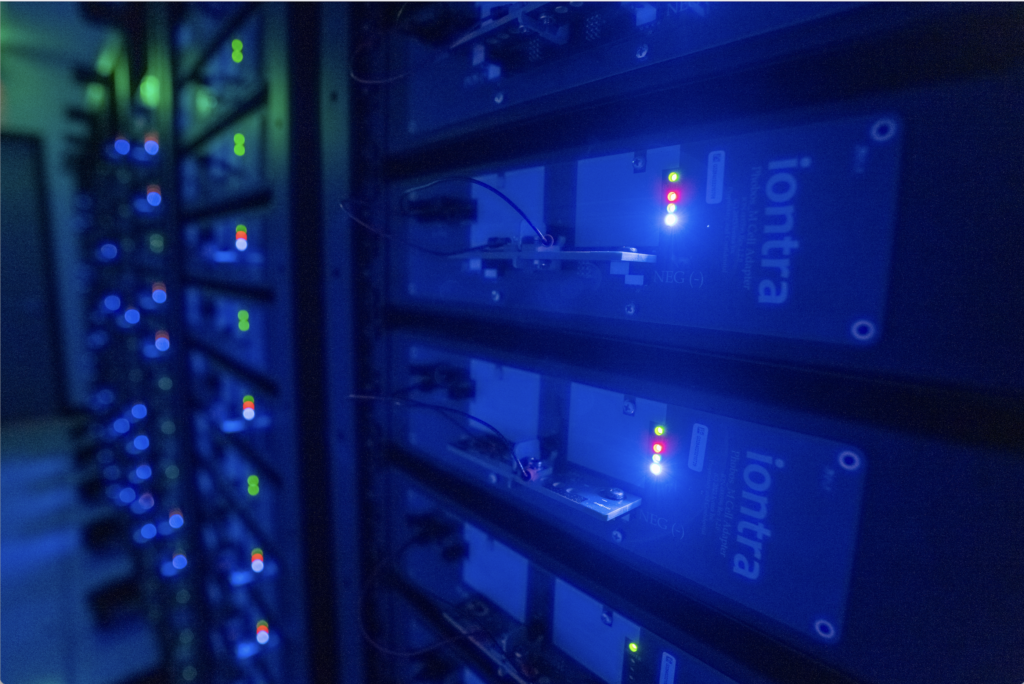
How Iontra achieves faster charge rates, today
At Iontra, we are not building new battery cells to deliver maximum efficiency and performance. We’re thinking outside the battery. Instead of modifying the battery’s components, or using new battery materials, we changed the way a battery is charged.
At its core, our technology is a charging protocol that can be added to the existing battery’s management system and directs the device on how to charge the battery in a way that achieves a desired result.
Remember when we talked about how uneven distribution can lead to plating and dendritic growth? By changing the way the battery is charged, we can minimize or even prevent this damage from ever occurring, which in turn increases the cell’s stability and extends its cycle life.
Using our advanced fast charging protocols, we have reduced charge times by 60% on some cells compared to their OEM’s spec sheets, and provided more than double the cell’s specified cycle life.
And the best part? We never had to modify the internal structure and chemistry of the battery. Whether our customers are looking to prioritize extended cycle life or faster charge speeds, these charge recipes are customized to meet their performance goals. This process is far less expensive than development and commercialization of new cells, and bypasses many of the costs that typically fall on the OEM because at the end of the day, there are no changes to the cell, only the way it’s charged.
These savings and immediate availability are essential factors to catalyzing wider adoption for electric vehicles. OEMs do not have to wait for a miracle chemistry to be discovered to start making meaningful strides towards mass electrification, and consumers, if this technology is implemented at scale, will not have to wait multiple hours for their vehicles to charge while their neighbors with internal combustion engines are in and out of the gas station in less than five minutes. Extreme fast charging is possible while maintaining energy efficient practices, and Iontra’s technology is the key.
Contact us to increase your charge speed in multiples, not percentages.